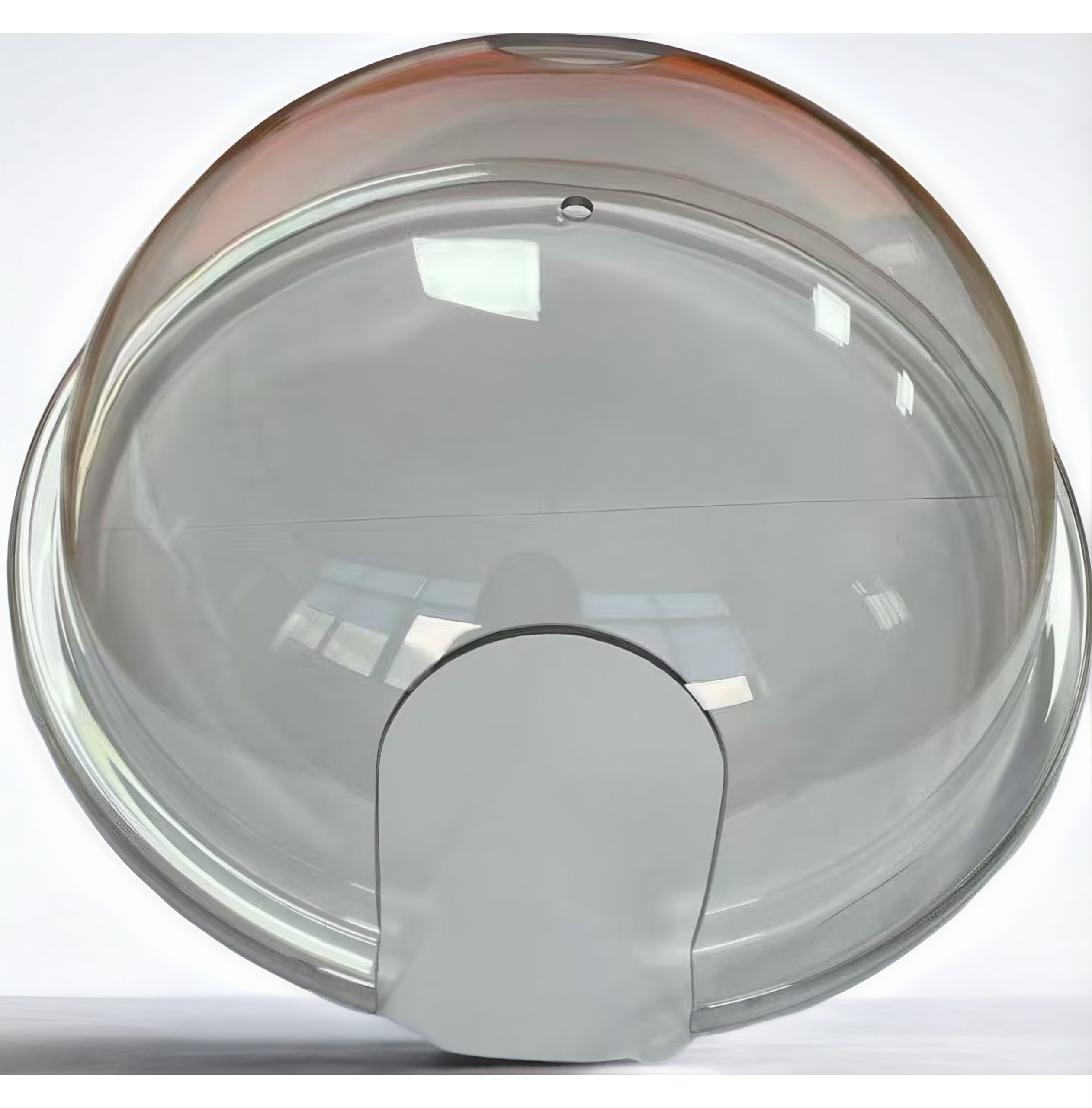
Successful Development of a High-Performance Transparent Lid for Testing Instruments
The client company is the top-ranking manufacturer of testing instruments in China (ranked #1). They required a lid for one of their testing instruments with specific properties: high temperature resistance (180°C), acid and alkali resistance, and transparency, so that the heating condition of the liquid inside the pot could be observed. After testing several materials, we finally chose PC. During the sample production process, we encountered issues such as small bubbles and scratches on the surface, which were not ideal. However, after optimizing the mold, material, and factory environment, we were able to produce a transparent product that passed the client’s testing successfully.
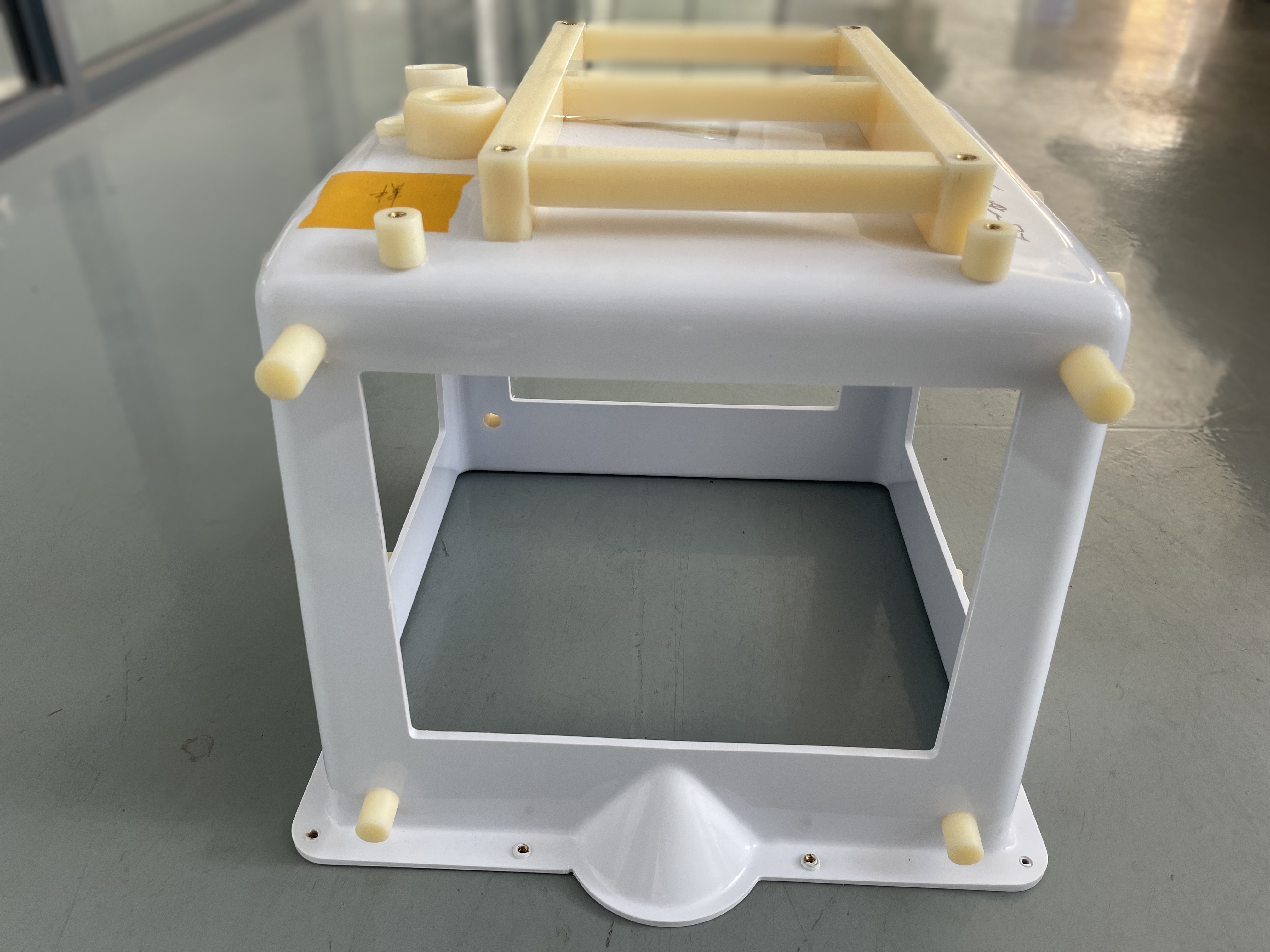
Precise Control in Food-Grade ABS Water Tank
The water tank in a Class III medical device of a medical company that is about to go public has a size of 345x366x306mm. It is required to use food-grade ABS material with a thickness of 5mm. The thickness of the hollow edges on all four sides must be uniform, and the upper and lower tolerances must not exceed ±0.2mm. Since the water tank needs to be waterproof, uneven thickness will lead to water leakage, so the process requirements are extremely high. The customer also requires the use of studs, nuts and water pipe interfaces during bonding installation.
During the initial machine adjustment process, we found that the bottom thickness was normal, but the thickness became thinner as it went up, which could not meet the customer’s requirements. After many debugging, the master adjusted the upper and lower molding processes, and the thickness of the final blister product was very uniform, which fully met the customer’s high standards. The customer was very satisfied with this and said that several other suppliers also participated in the quotation, but they all thought that this thickness requirement was difficult to achieve. In the end, our process capabilities and product quality won the recognition of customers.
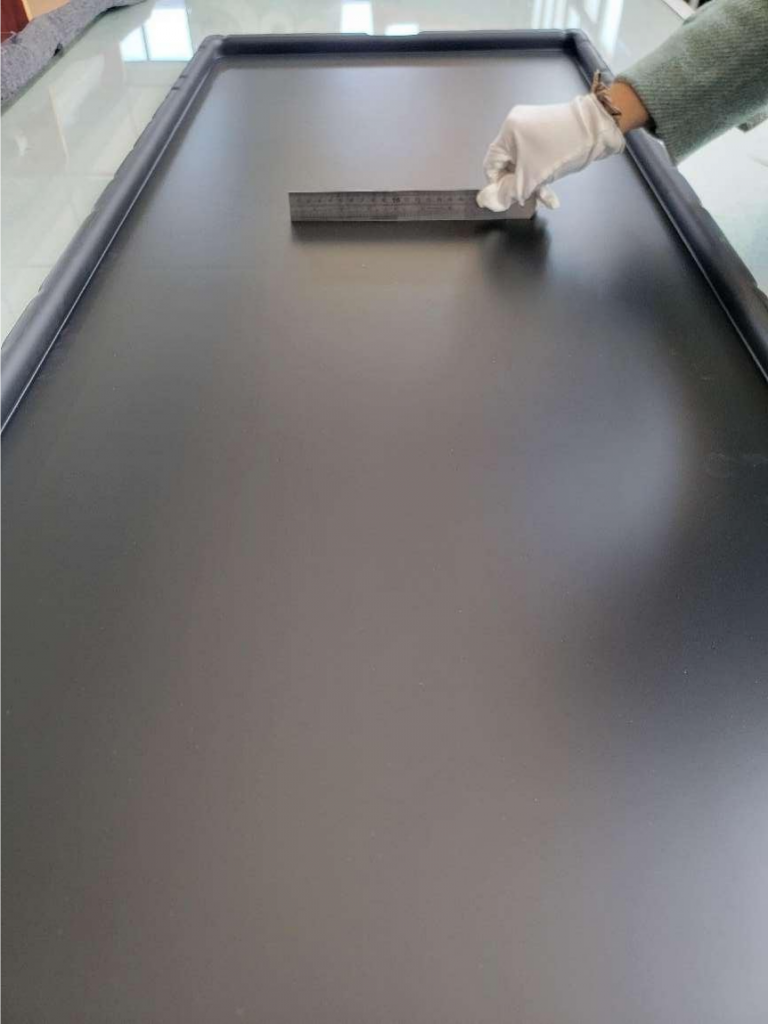
Solving Surface Issues of Anti-Static Trays and Gaining Customer Trust
A company that manufactures anti-static trays contacted us in April 2024 to custom-make trays for them. However, due to a price difference with their existing supplier, they initially chose not to proceed with us. In November, the customer reached out again and requested a sample. During our discussion, the customer mentioned that their current supplier’s trays had the following issues: 1. Slight deformation due to the elongated design; 2. Surface imperfections such as particles, crystallization points, and scratches; 3. Uneven surface. The customer asked if we could resolve these problems. Based on our stringent material requirements and the affirmation from our experienced technicians, we confirmed that we could address these issues. The next day, the customer brought a mold sample to us. After sampling and confirmation, the customer approved the sample and placed an order for production. Subsequently, they also entrusted us with several other tray designs. During production, the customer sent a team to conduct full inspections, measuring the glass surface with a level. The final product passed with a 99.5% success rate.
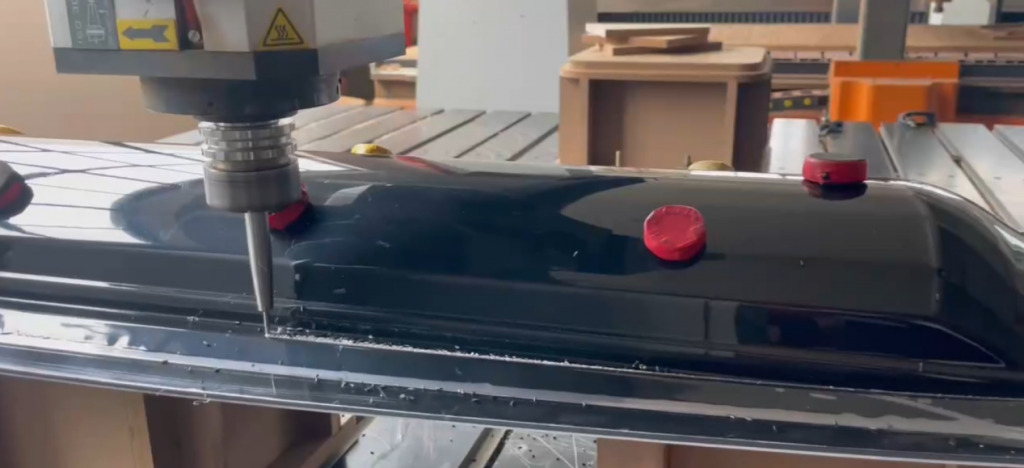
Precise Manufacturing Solves Car Roof Sunshade Box Assembly Issues
A customer specializing in automotive outdoor accessories contacted us to customize a sunshade box for the car roof, with dimensions of 1288*200mm. The wall width of the upper and lower shells needed to be controlled within ±3mm, and the wall thickness also required a tolerance of ±3mm. Any dimensional discrepancies would cause gaps between the upper and lower shells, leading to issues with the assembly of other components and injection-molded parts. Moreover, water could seep into the box, potentially damaging the internal motor. The customer had previously worked with another factory, but frequent errors led to rework or modifications to the parts. Given the elongated shape of the shell, slight deformation during production could cause uneven edges. Through the expertise and adjustments of our engineers with 20 years of experience, we successfully ensured uniform wall thickness and straight edges, making the assembly process much smoother for the customer.